Air Conditioning Maintenance and Records – Legislation – Your Responsibilities
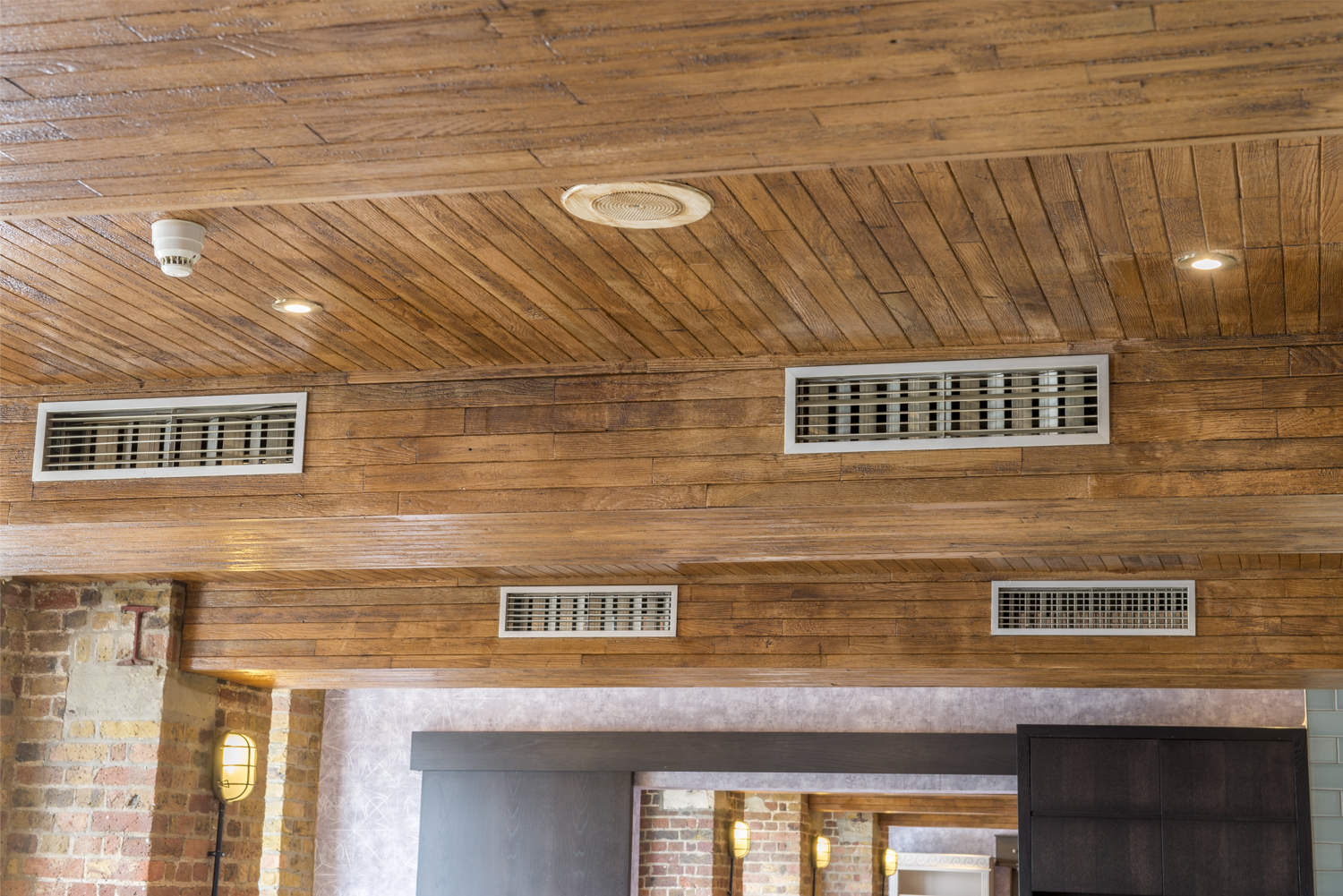
Estimated reading time 11 minutes
When it comes to the operation of refrigerant based air conditioning there are legal and legislative requirements / statutory obligations and duties of care in the operation and maintenance of air conditioning systems that the person who controls the operation of the system, such as the building owner or manager are required to comply with by law. These cover everything from air conditioning maintenance and performance to documentation and inspections.
Why Are Air Conditioning Inspections Required?
There are numerous reasons as to why it’s important to have your air conditioning system inspected by a qualified, experienced air conditioning engineer:
- to provide healthy and comfortable environments for anyone using your building
- to ensure your air conditioning system is working as it should
- ensuring the air conditioning system equipment is safe
- to catch issues early and resolve them before your system fails
- to improve energy efficiency, reduce the amount of energy your air conditioning system uses and reduce costs
- to look for ways to improve the system
- to limit or stop the escape of refrigerant gases
- to advise on replacement of older systems where the refrigerant in use can no longer be replaced, where the system is no longer energy efficient or where it is oversized and where a new system would provide benefits
Below are the various legal responsibilities, directives and regulations for people managing air-conditioning systems.
The Energy Performance of Buildings Directive
The UK government have provided guidance over air conditioning inspections in buildings.This guidance is for people managing air-conditioning systems to enable them to meet the requirements of the Energy Performance of Buildings Regulations (PDF).
According to gov.uk this guidance is “intended to help anyone who manages or controls an air-conditioning system to understand how the Energy Performance of Buildings Regulations (Certificates and Inspections (England and Wales) Regulations made and the Directive, on which these regulations are based, work in practice, how to apply the regulations, what their responsibilities are and when air conditioning inspections are required.”
It’s important to note that the gov.uk guidance explains how the Energy Performance of Buildings Directive requirements work in practice, it is offered only as a guide. It’s important that business owners read and understand the regulations and understand whether they have air conditioning equipment which falls within the requirements of the regulations. Where there is any doubt you should seek independent legal advice.
Equally important to note is this guidance only addresses Energy Performance of Buildings Regulations. Other statutory inspection requirements including health and safety, F-gas Regulations and associated requirements, are outside the remit of this directive.
The Energy Performance of Buildings Directive states that from January 2011 all air conditioning systems with an effective rated output of more than 12kw must be regularly inspected by an energy assessor and have a CIBSE TM44 energy efficiency assessment carried out.
This includes systems consisting of individual units which are less than 12kW but whose combined effective rated output is more than 12kW. The guidance states that “the effective rated output is the maximum calorific output in kW stated by the manufacturer of the system as deliverable during continuous operation while complying with the useful efficiency indicated by the manufacturer. One or more air conditioning units within a building controlled by a single person are considered to comprise a single air conditioning system for the purposes of the regulations. The person who controls the operation of the system is the person who controls the technical functioning of the system, not someone who can just adjust the temperature or whose only responsibility is to adjust the controls.”
How Often Should Inspections Be Carried Out?
The regulations state that the first inspection of the air conditioning system must be carried out as follows:
- for all systems first put into service on or after 1 January 2008, the first inspection must have taken place within five years of the date when the system was first put into service
- for other air conditioning systems, where the effective rated output is more than 250kW the first inspection must have taken place by 4 January 2009
- for other air conditioning systems, where the effective rated output is more than 12kW the first inspection must have taken place by 4 January 2011.
The inspection is a legal requirement. There must be no more than 5 years between inspections and inspections must be carried out by an accredited energy assessor who is registered on the Non-Domestic Energy Performance Certificate Register (NDEPC). A copy of the inspection report must be kept. The person who controls the technical functionality of the system, usually the owner, office manager or facilities manager is responsible for ensuring the business maintains an up-to-date TM44 inspection schedule and report.
Protecting the Planet
Refrigerants used in air conditioning systems and refrigeration caused damage to the ozone layer.
The ozone layer contains the highest concentration of ozone in relation to other parts of the atmosphere and is the region of Earth's stratosphere that absorbs most of the Sun's ultraviolet radiation thereby preventing the most harmful wavelengths of ultraviolet (UV) light from passing through the Earth's atmosphere. When Chlorofluorocarbons (CFCs) come into contact with ozone in the stratosphere, they destroy ozone molecules. One chlorine atom can destroy over 100,000 ozone molecules before it is removed from the stratosphere. This is a global warming effect of up to 23 000 times greater than carbon dioxide (CO2).
It is because of this that the EU came together to agree the Montreal Protocol.
The Montreal Protocol
The Montreal Protocol, an international treaty designed to protect the ozone layer by phasing out the production of numerous substances that are responsible for ozone depletion, was brought in to deal with this threat to the ozone layer. The plan includes the production and consumption of ozone-depleting substances, was signed in 1987 and entered into force in 1989.
F-gas Regulation
In 2006 the European Union brought in the F-gas Regulation. The current F-gas Regulation, which has applied since 1 January 2015, replaces the original F-gas Regulation adopted in 2006. The framework set out by the regulation and its supplementary European Community Regulations is underpinned in Great Britain by the Fluorinated Greenhouse Gases Regulations 2009 (SI 2009/261).
The current EU regulations specify:
- the total amount of the most important F-gases that can be sold in the EU from 2015 onwards will be limited and they will be phased down in steps to one-fifth of 2014 sales in 2030.
- the banning of the use of F-gases in many new types of equipment e.g.in fridges in homes or supermarkets, air conditioning and foams and aerosols where less harmful alternatives are widely available.
- preventing emissions of F-gases from existing equipment by requiring checks, proper servicing and recovery of the gases at the end of the equipment's life.
In 2018 the European Union ratified the Kigali Amendment to the Montreal Protocol which aims to bring about a phase down on a global level of hydrofluorocarbons (HFCs) gases. The phase down is expected to begin sometime in the 2020’s.
Remaining F-gas compliant is a legal obligation for any business that operates an air conditioning system with a CO2 equivalent charge of 5 tonnes or more.
As mentioned previously one of the main aims of the F-gas regulations is to minimise F-gas emissions through requiring checks, proper servicing, repair and recovery of the gases at the end of the air conditioning system's life. As with the Energy Performance of Buildings Directive the person who controls the technical functionality of the system, usually the business owner, office manager or facilities manager is responsible for ensuring compliance with the regulation and are required to have any equipment within the F-gas specifications leak tested.
They must also make sure that there is a record of maintenance and servicing. Any air conditioning engineers and companies must have the appropriate certification to be allowed to undertake work on air conditioning systems. They must hold a Department for Environment, Food and Rural Affairs (DEFRA) approved Stationary Equipment Qualification Company Certificate (full certificate), issued by Refcom.
All of the obligations can be found on the Department for Environment, Food and Rural Affairs (Defra) Fluorinated gas (F gas): guidance for users, producers and traders page.
Frequency of F-gas Testing
The frequency of F-Gas testing is required as follows:
- 5-50 tonnes and above – at least every 12 months
- 50-500 tonnes and above – at least every 6 months
- 500 tonnes and above – at least every 3 months
F-gas leak checking depends on the amount of F gas in the equipment and the global warming potential of the F gas (how much the F gas contributes to global warming). Your air conditioning system should be labelled with information on the amount of F-gas it contains, but if you cannot find this you can estimate it using the calculator provided by UK Government to express the mass of a fluorinated greenhouse gas (F gas) in terms of CO2 so that you comply with F-gase regulations.
If you install a system which allows automatic detection of F-gas leaks, you can double the period of time allowed between leak checks. If your equipment contains an F-gas equivalent of 500 tonnes or more of carbon dioxide then you must fit a leak detection system.
Air Conditioning Maintenance and Service Records
Anyone who operates stationary refrigeration equipment, stationary air-conditioning equipment, refrigeration units of refrigerated trucks and trailers containing an F-gas equivalent of 5 tonnes or more of carbon dioxide must keep records about the equipment you operate or service.
Records must be kept for 5 years on the:
- quantity and type of gas in the equipment when it’s installed, added during maintenance (for example in leak repairs) or recovered/reclaimed
- identity of the company and air conditioning or refrigeration engineer carrying out servicing
- what you’ve done to recover and dispose of gas e.g. you should record the name, address and certificate number of the recycling or reclamation facility must also be recorded or the registered waste carrier you use to dispose of it
- you must also keep records of the name, address and certificate number of any companies used to install, service or decommission your equipment
- dates and results of all mandatory leak checks and the equipment it applies to
Note: The withdrawal of the United Kingdom from the EU took effect on 1 February 2020. From that date, the United Kingdom is considered to be a third country (A country that is not a member of the European Union as well as a country or territory whose citizens do not enjoy the European Union right to free movement, as defined in Art. 2(5) of the Regulation (EU) 2016/399 (Schengen Borders Code). However, during the transition period, which ends on 31 December 2020, the F-Gas Regulation (EU) No 517/2014 continues to be applicable to and in the United Kingdom.
Professional M&E Contractors
Given the implications of ensuring your business is meeting its legal obligations in terms of the Energy Performance of Buildings Directive and F-gas compliance it’s important for business owners, facility and office managers fully understand their responsibilities. By contracting with a professional air conditioning and refrigeration company with in-house expertise in both HVAC and electrical engineering and fully qualified to carry out full maintenance, servicing and record keeping you can be sure that your business is fully covered and fully compliant.
Additionally ensuring your HVAC is properly maintained will not only prolong the lifespan of your system but it will also help to ensure that your air conditioning or refrigeration system, as a whole and its individual parts, will continue to work efficiently and effectively day in and day out, saving you time and money in the long run.
Synecore
Synecore is a professional air conditioning maintenance company offering air conditioning and commercial refrigeration systems Planned Preventative Maintenance (PPM). Each PPM package is specifically designed to meet the needs of individual businesses and to ensure full F-Gas compliance.
To find out how Synecore can help your business, get in touch with our head office in Sittingbourne, Kent to discuss your requirements and arrange your free no obligation quotation at your convenience. We operate throughout Kent, London and the UK. You can call us on 01795 509509, get in touch via our contact form or chat with us via our chat form.