Heating, Ventilation and Air Conditioning Maintenance Saves Energy – Cuts Bills
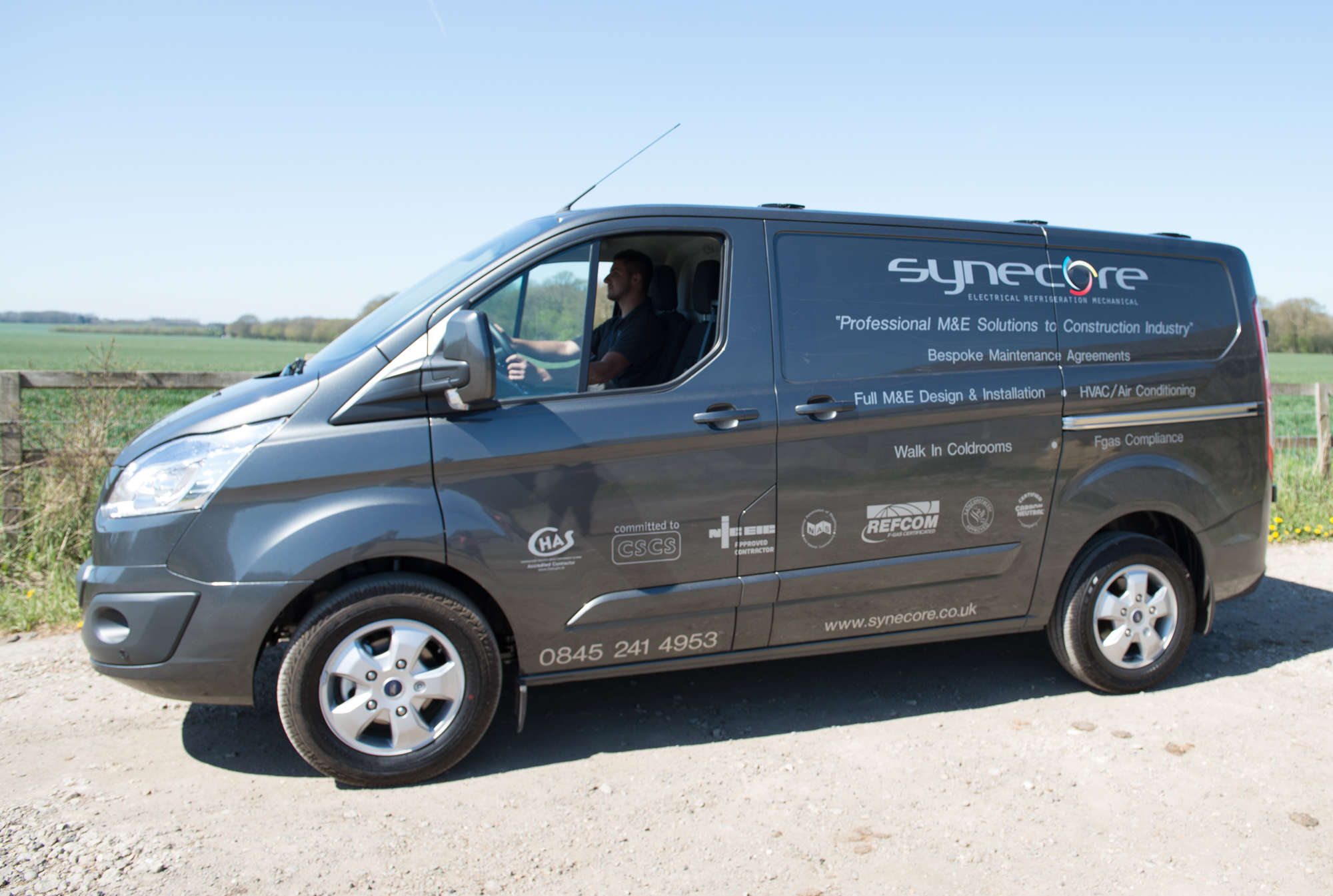
Estimated reading time 6 minutes
When it comes to business, companies have to make day to day decisions on where to spend money. In many cases air conditioning maintenance may not be a priority or may be underfunded, especially when an HVAC system is first installed or when everything seems to be working as it should.
We know, from numerous studies, that when all the factors that go towards your energy bills are factored in e.g. extending the life of your HVAC, ensuring the system is working efficiently resulting in the reduced use of energy, less downtime, fewer interruptions to building operations thereby ensuring the continued comfort of your staff and visitors heating - ventilation and air conditioning maintenance can save energy – resulting in lower energy bills.
Effective proactive (preventative) air conditioning maintenance can cut costs between 5% and 50% depending on the HVAC system and components when compared to businesses that maintain their HVAC equipment reactively.
How Air Conditioning Maintenance Impacts Energy Efficiency
Here are a few of the reports that explain how maintenance impacts energy efficiency and the life of your HVAC system.
According to the Indoor Air Quality Association (IAQA) regular HVAC maintenance can reduce breakdowns by as much as 95% and planned preventive maintenance can help to ensure that your HVAC system is running efficiently thereby reducing your energy bill by up to 30%.
Facilitiesnet highlight that “one of the easiest benefits to document is how HVAC maintenance affects energy efficiency. Facilities in which proper HVAC maintenance is completed will use at least 15 to 20% less energy than those where systems are allowed to deteriorate” and “reactive maintenance is the most costly way to maintain building HVAC systems... organizations that have implemented comprehensive maintenance programs find that their total costs can be as much as 50% lower than the costs for those organizations that continue maintain equipment reactively.”
The Institute for Buildings Efficiency looked at a number of studies “that quantified energy savings from maintenance” into two categories. These were: analysis of failures in individual HVAC components including reduced condenser flow rate, sub-optimal refrigerant levels, leaks in the compressor; air flow, thermostat and sensor issues, how their failure could impact efficiency and the energy savings possible by correcting those failures and whole-system estimates based on interviews with HVAC maintenance experts. There studies included:
The New Buildings Institute which found that maintenance can reduce energy use by 10-20%. In contrast, lack of maintenance can increase energy use by 30-60%.
The Portland Energyconservation inc. (PECI) found that maintenance aimed at maintaining the efficiency of HVAC and lighting systems helped to decrease energy bills 5-20% without an outlay of significant capital investment.
Air Conditioning Maintenance Types
It’s clear that air conditioning maintenance is vital for the smooth and efficient working of an HVAC system. There are a number of different maintenance paths that companies can take outlined below:
Reactive maintenance is where an HVAC is run until a failure or issue occurs that requires intervention. With a purely reactive maintenance plan there are no costs until something breaks down or starts to have issues. However, although this may seem like a way to make cost savings in the short term it’s usually the most costly way to maintain an HVAC system and a false economy that can result in bigger problems and higher bills in the longer term.
Predictive maintenance, otherwise known as condition-based maintenance, is based on the condition of the system and uses visual inspections and data from the building management system and sensors to try to determine when maintenance will be required rather than on a planned schedule. Limits are set and anything outside of these automatically alert the building management system that there is a potential issue. The downside to predictive maintenance is that an issue can be missed or goes on for longer than is good for the system and results in damage and larger repair costs. There is also the initial cost of setting up the system and technology to monitor for issues and working out the limits to set to catch issues before they become major problems. Where visual inspections are used to predict problems staff also need to be trained to spot problems before they become larger issues.
Planned preventative air conditioning maintenance runs to a schedule which is defined by the age of the HVAC, size and type of system. This type of maintenance is proactive and any work can be scheduled in advance. It ensures that components and the system as a whole are maintained to ensure efficiency. Equipment lifetime is usually extended and the reliability of your HVAC system is increased which in turn results in lower costs. Given the current energy crisis and increasing fuel bills ensuring your HVAC is running optimally and efficiently can only be a good thing.
Air Conditioning Maintenance – More Than Maintaining Your HVAC
HVAC maintenance is more than just keeping your HVAC running reliably. There is also the matter of remaining F-Gas complaint which is a legal obligation for any business that uses an air conditioning system with a CO2 equivalent charge of 5 or more tonnes. Failure to comply with F-Gas regulations can result in significant penalty charges for operators, therefore it is vital that your system is regularly maintained and serviced and detailed service and maintenance records are kept by a professional air conditioning maintenance engineer.
Where your HVAC is reaching its end of life and is 15 years or more it could be using R-22 HCFC refrigerant. R-22 was commonly used in air conditioning and refrigeration systems prior to 2003, but due to its harmful effect on the ozone layer, it was made illegal to even top-up or replace the gas as of January 2015. As a result the service, maintenance and recycling of R-22 HCFC in any refrigeration and air conditioning system is prohibited and leaks can result in your system failing and becoming unusable. It’s vital in older systems that R-22 monitoring forms part of any maintenance carried out on the system.
Air conditioning systems with a rated output of 12kW or more require a CIBSE TM44 energy efficiency assessment of a buildings air conditioning to be carried out. This includes systems consisting of individual units with less than 12kW, but combined have an effective rated output of more than 12kW. There cannot be more than five years between each inspection, which must be carried out by an accredited energy assessor.
Synecore Building Planned Preventative Maintenance
Synecore offer air conditioning planned preventative maintenance packages to suit your air conditioning system. We cover Kent, London and across the UK. Our maintenance projects are overseen by an experienced project manager so you know you are in good hands.
If you would like to learn more about how to keep your air conditioning system in top shape, through a PPM, contact Synecore on 01795 509 509. Our team will book an appointment for one of our engineers to visit your site and discuss your options.